Analytical Engineering, Inc. offers development of prototype hardware in our test cells utilizing engine testing methods that include both industry standard and custom developed cycles. AEI has designed, built, and installed a variety of stands for component development and evaluation. These development rigs are operated and monitored according to development plans cooperatively developed with the customers. HALT and HASS development is available as well as durability bench development, environmental development, thermal development and altitude development. Data acquisition is almost limitless at AEI due to our in-house electrical engineering and controls software.
- Custom-designed rigs for rapid, cost-effective component development
- Simulation of temperature, pressure, flow rates and vibration conditions for component development
- Cooperative rig design and test planning
- In-house rig construction using AEI engineering and skilled fabrication resources
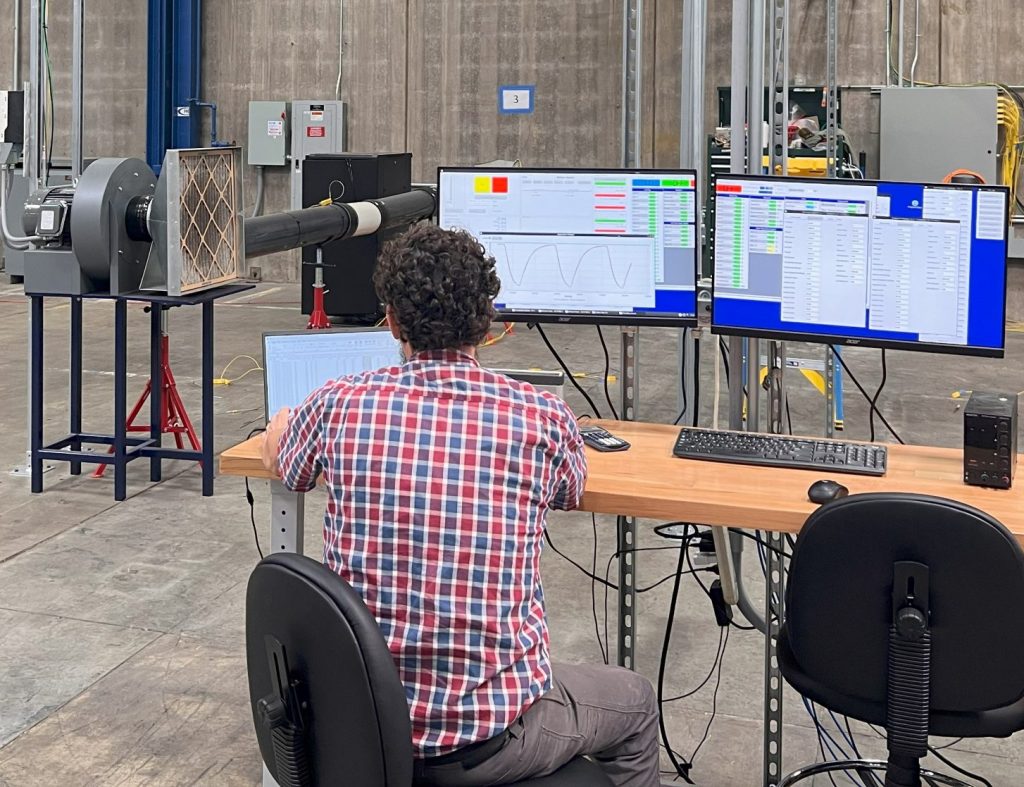
Electric Heater Test Bench & Flow Benches
At AEI, our air flow rigs are engineered to meet the demanding requirements of modern testing environments, providing precise control and robust performance for a wide range of applications. Designed with state-of-the-art technology, our rigs deliver the reliability and flexibility needed to support cutting-edge research and development.
Key Features of AEI Electric Heater Test Benches
- High Air Flow Capacity
Our air flow rigs are capable of supplying up to 14 kg/min of air, ensuring sufficient flow rates for even the most rigorous testing scenarios. Whether you’re conducting advanced thermal management tests or simulating real-world conditions, our rigs provide the airflow necessary to achieve accurate and repeatable results. - Powerful Electrical Supply
Each rig is equipped with a 48V power supply, delivering 270 amps to support high-powered equipment and demanding applications. This robust power capability allows for consistent operation, even under extreme testing conditions, ensuring that your experiments are never compromised by power limitations. - Automated Operation for Efficiency and Accuracy
Our flow rigs are completely automated. This automation not only increases efficiency but also enhances the accuracy and repeatability of your tests, providing reliable data every time. - Custom Options available
While our current capabilities are outlined, we are always eager to explore new opportunities and tackle new challenges.
Key Features of AEI Flow Benches
- High Air Flow Capacity
Our air flow rigs are capable of supplying up to 2000 cfm of air, ensuring sufficient flow rates for even the most rigorous testing scenarios. Whether you’re conducting advanced thermal management tests or simulating real-world conditions, our rigs provide the airflow necessary to achieve accurate and repeatable results. - Automated Operation for Efficiency and Accuracy
Our flow rigs are completely automated. This automation not only increases efficiency but also enhances the accuracy and repeatability of your tests, providing reliable data every time. - Custom Options available
While our current capabilities are outlined, we are always eager to explore new opportunities and tackle new challenges.
Burner Rigs
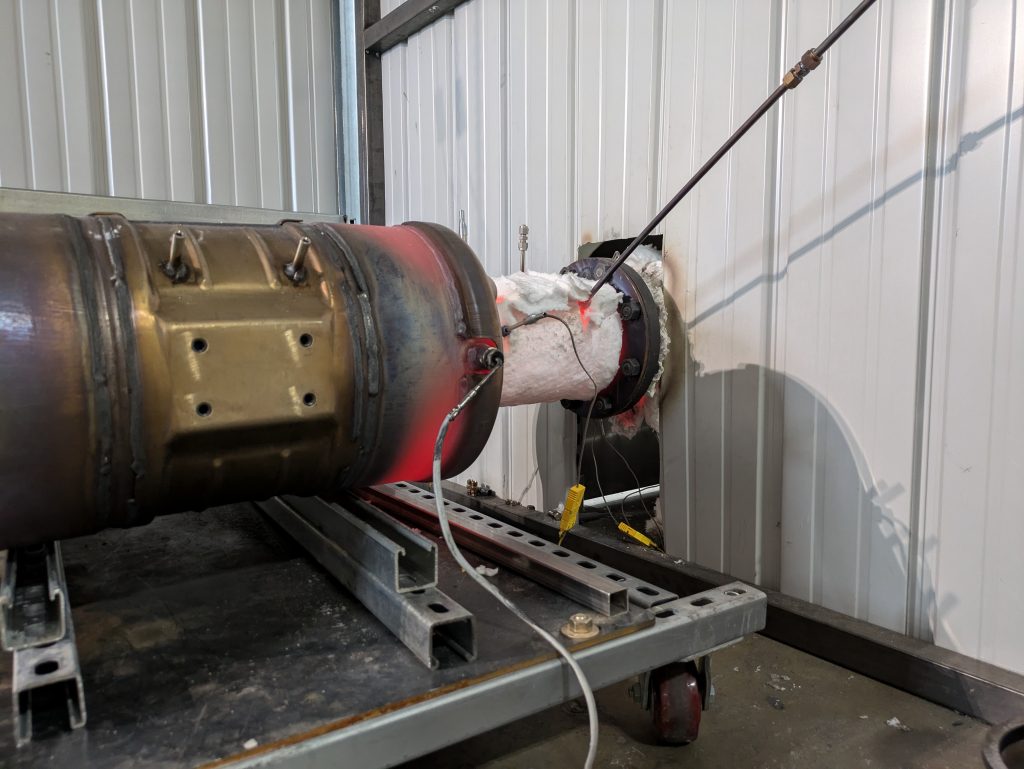
At AEI, our burner rigs are designed to push the boundaries of testing, providing the high-temperature and high-flow capabilities necessary for advanced aftertreatment and thermal management research. With precise control over airflow and temperature, our burner rigs enable you to simulate the most demanding conditions and achieve reliable, accurate results.
Key Features of AEI Burner Rigs
- Wide Range of Air Flow Rates
AEI’s burner rigs can supply an air flow rate ranging from 2.5 kg/min to 30 kg/min, offering the flexibility to conduct a variety of tests. Whether you need low-flow conditions for detailed analysis or high-flow scenarios to simulate real-world challenges, our rigs provide the control you need. - Extreme Temperature Capabilities
Our burner rigs can reach temperatures up to 1000°C, making them ideal for testing the limits of aftertreatment systems. This high-temperature capability is crucial for evaluating system performance under the most extreme conditions, ensuring that your components can withstand the heat. - Versatile Testing Environments
AEI burner rigs are designed to accommodate a wide range of aftertreatment systems. Whether you are testing catalytic converters, DPFs, SCRs or other critical components, our rigs provide the necessary conditions for thorough and reliable testing. - Custom Options available
While our current capabilities are outlined, we are always eager to explore new opportunities and tackle new challenges.
Why Choose AEI Burner Rigs?
- Precision and Control
With advanced control systems, our burner rigs offer precise regulation of both airflow and temperature, ensuring that your testing environment is exactly as needed for each experiment. - Reliability and Durability
AEI burner rigs are built to handle the most demanding testing scenarios. With robust construction and high-quality components, our rigs deliver consistent performance even under extreme conditions.
Applications
AEI’s burner rigs are ideal for a variety of applications, including:
- High-temperature material testing
- Testing and development of aftertreatment systems
- Thermal management research
- Component durability testing under extreme conditions
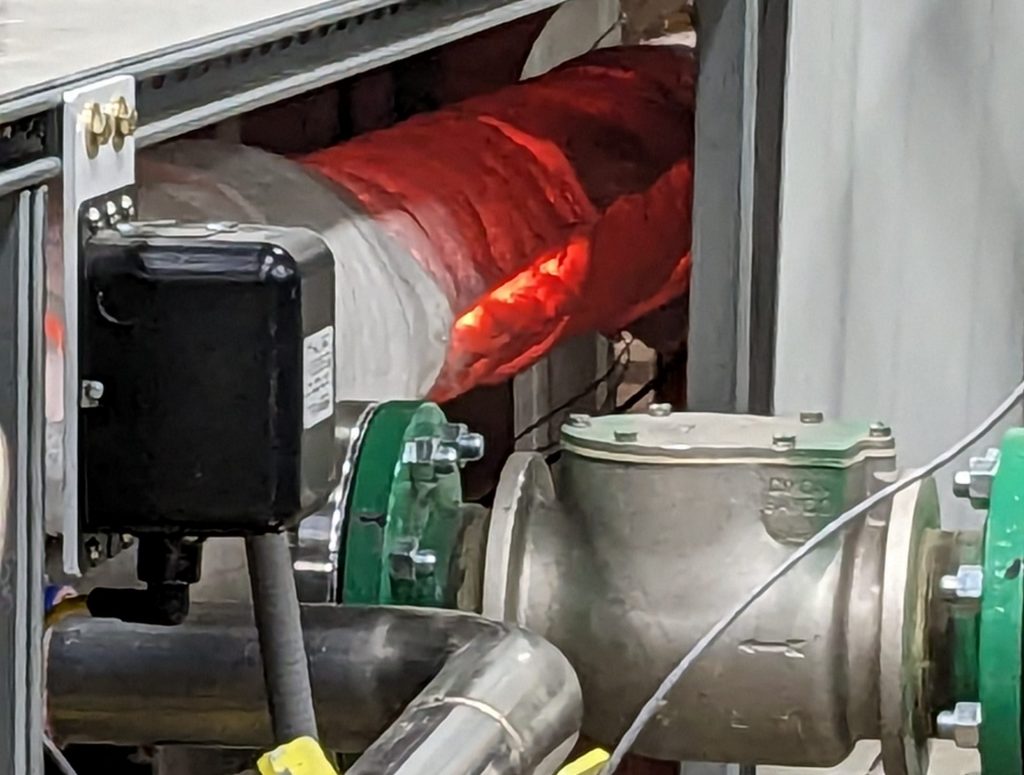
Engine Thermostat Development
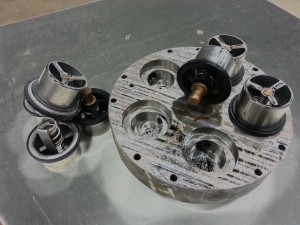
A thermostat is a good example of a component that may be cyclically developed without the need for installation in an engine. Many thermostats can be simultaneously developed with a custom designed development stand at a cost significantly less than an equivalent engine development. AEI has designed and constructed a dedicated development rig for coolant thermostats. This development stand has been utilized several times to validate new suppliers or design changes by thermally cycling five thermostats through at least thirty thousand repetitions, while stopping the development to check for length of stroke at a pre-determined number of cycles throughout the validation process. In this instance, a cycle is defined as fully opening the thermostat with 220°F fluid, then decreasing the fluid temperature to 160°F to close the thermostat.
EGR Cooler Durability
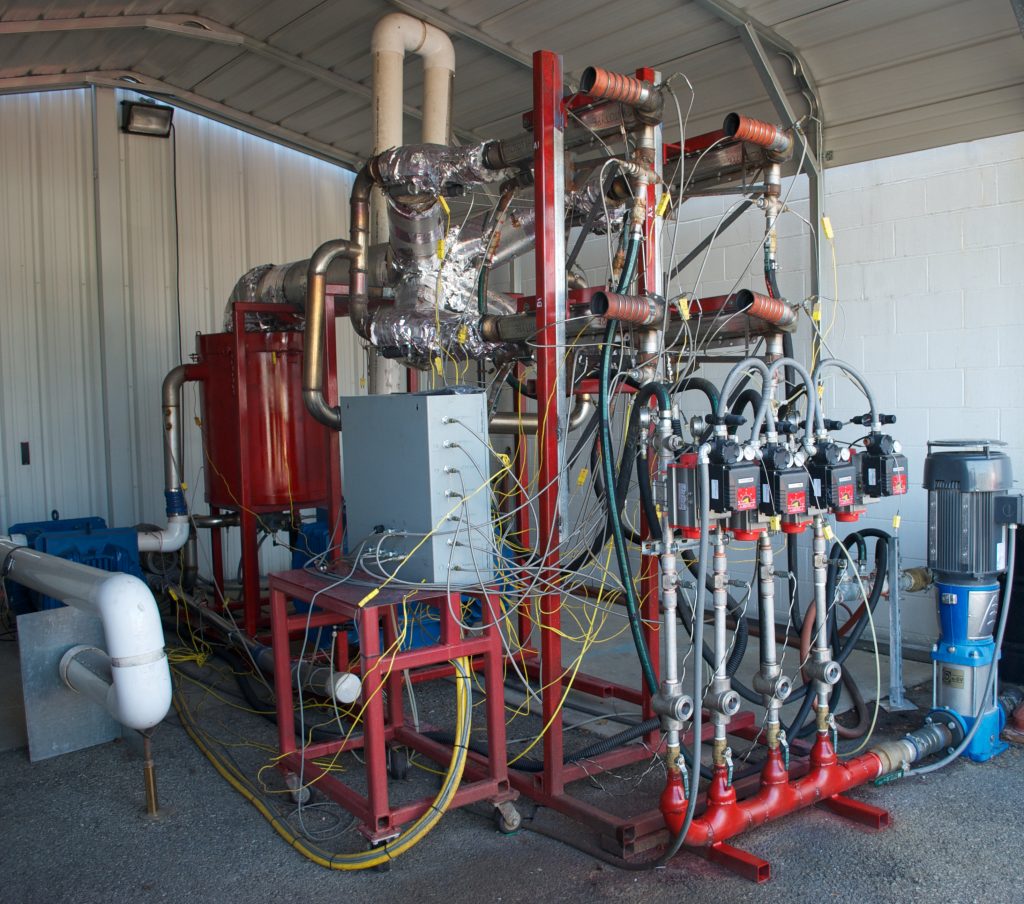
AEI designed and built a development stand that simultaneously tests four EGR coolers. These coolers were subjected to temperature extremes on the exhaust gas and coolant sides, simulating thermal expansion, contraction, and pressures. The coolant and gas flow rate could be modulated to achieve different heat transfer scenarios. This stand has been utilized to develop EGR coolers up to 50,000 thermal cycles. Temperature, pressure, and flow rate information was recorded at one hertz so that the performance could be tracked over time.